What is AC Drive Reconstruction for Oil Industry Company
Reconstruction purpose
In order to lower production cost and power consumption, variable frequency technology should be adopted.
By utilizing low voltage AC drive, the plant has gained considerable energy saving effect and maintenance experience. With maturity of medium voltage AC drive, we utilize this technology outcome to medium voltage motor. We reformed for three fans.
Parameters of fans
Fan | Rated voltage | Rated current | Rated power | Power factor | Rated speed | |
PA fan | 6000V | 131A | 1120kW | 0.85 | 1490r/min | |
SA fan | 6000V | 94A | 800kW | 0.85 | 1490r/min | |
1# ID fan | 6000V | 61A | 500kW | 0.85 | 990r/min |
Reconstruction scheme
1. AC drive selection
After comparing and analyzing, the plant selected Iacdrive AC drive eventually.
2. Main circuit
We decided to adopt “one drive one” scheme due to importance of fan. That is, one AC drive drives one motor of fan. In order to improve reliability and safety, we add bypass circuit. Please see the figure.
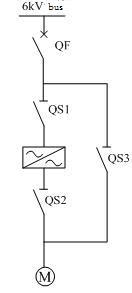
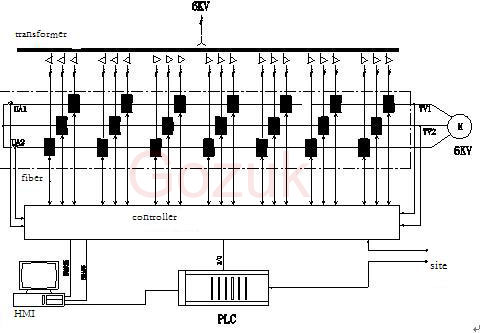
QF is vacuum breaker. QS1, QS2 and QS3 are medium voltage isolator. Medium voltage AC drive is between QS1 and QS2. QS3 is bypass switch. When motor needs to run in variable frequency, open QS3 and close QS1, QS2, then close QF. When motor needs to run in direct on line, open QS1, QS2, close QS3 and then close QF. In this way, motor can run in direct on line during AC drive downtime or maintenance.
Above scheme is typical manual scheme. QS2 and QS3 interlock in mechanism and they cannot close simultaneously.
In order to realize fault AC drives protection, AC drive sends trip command when it faults seriously and link trips medium voltage breaker to make AC drive off power. In the meantime, three switches interlock electrically with QF. Only when breaker is off, can personnel operate switch, which ensures safety.
3. Control scheme
According to actual state, we adopt three control schemes. They are DCS close loop control, DCS open loop control and local control.
4. Cooling scheme
Principle of AC drive is to rectify AC to DC and invert DC to AC. During this course, electric components emit heat (2%). The heat causes equipment temperature up and damages equipment. In order to ensure stable work of AC drive, the heat must be dissipated outside. So cooling scheme is very important. After researching carefully, we adopt the most effective and easiest scheme—air cooling. Install air duct on top of AC drive. The duct discharges the heat outside. The scheme only needs a duct without other device, so it is simple and reliable with few failure factor. Make full load test at 40℃. Max temperature of AC drive reaches to 68℃. Compared with max design temperature-rising, the result is ideal.